The requirement:
North American Industry required large volumes of disposal medical masks to be procured and imported into North America for distribution to schools before re opening after the July summer holidays.
These medical masks were to meet FDA standards and have approval prior to importing.
Finally, they needed to be manufactured then shipped into the approved warehouse in Los Angeles, California, of our logistics partner – FDA.
The challenge:
To lock in a manufacturer to produce:
- To a guaranteed schedule
- Ensure the production would meet FDA standards, including labelling and packaging.
Just over one year into the pandemic, the availability of sea freight shipping containers and reliability of shipping times was in a die state.
It was the worst time in history for managing global shipping logistics, with unprecedented and unpredictable delays.
In addition, the sea freight was ten times what these costs had been in 2019, pre the pandemic.
Not only were scheduled sailing times pushed out, but actual wait times for vessels to berth and unload in North American ports was adding a further 3- 6 weeks.
Added to this, trucking times to collect shipping containers from North American ports once freight cleared customs was a further 1-2 weeks due the shortage of truck drivers.
Solution:
Due to our long term industry connections and solid relationships, we had already procured factories in Asia that met all the Australian requirements, and were able to then confirm that this pre vetted factories for FDA approval.
To be more efficient with sea freight costs we locked and loaded 40 foot containers at the factory with cartons that had no pallets to maximum volume loading.
We requested independent, international testing and SGS reports specific to their FDA certification for export and import.
We used our sea freight logistics partners to guarantee container allocation including vessel space on pre locked sailing schedules.
We arranged sea freight only shipping via the fastest sea freight route into North America, the port of Long Beach, California.
We pre-arranged warehousing with our North American distribution logistics partner to distribute from their FDA approved warehouse. This also included access to other FDA approved warehouses if required in additional locations that would cover both the west and east coast of North America.
We prescheduled container collection direct with the trucking company to collect from the port and deliver directly to the distribution warehouse of our logistics partner located close to the Port of Long Beach
Our logistics partner unloaded the containers and palletised the loose cartons on US sized pallets ready for distribution.
Only using pre logistics partners allowed us to have guaranteed shipping container allocation and locked space of shipping vessel.
Conclusion:
✔ We secured a factory with FDA approval in North America
✔ We produced the medical masks to FDA standards and shipped to the port of Long Beach as per schedule allowing for shipping delay times in our delivery planning.
✔ We cleared customs in the port of Long Beach California
✔ We promptly delivered into California FDA approved warehouse ready for immediate distribution
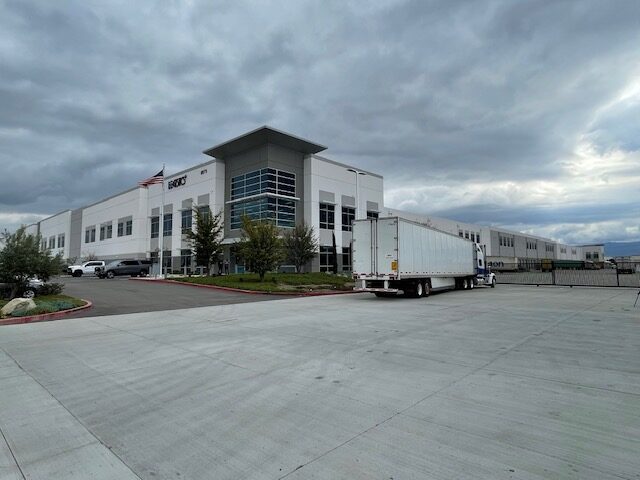
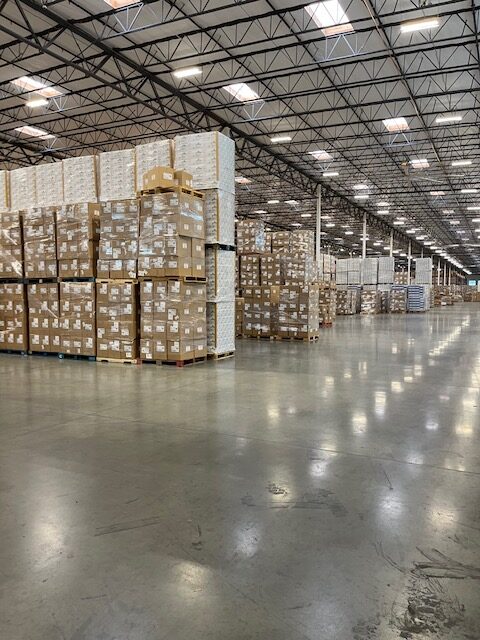
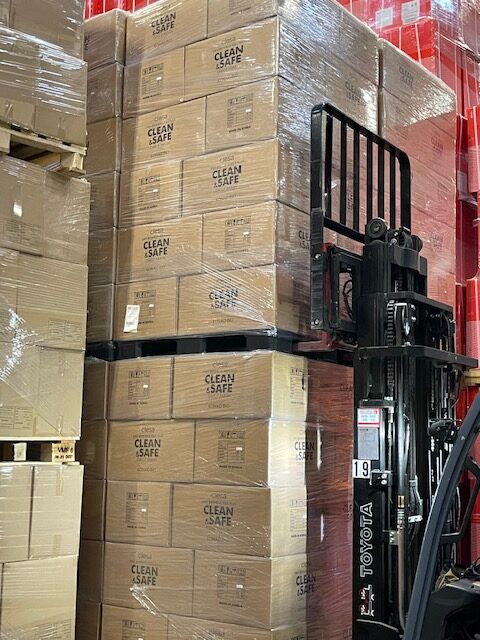
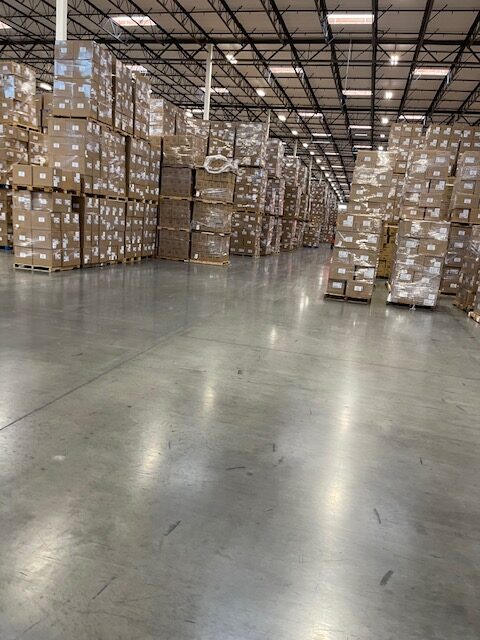